This article aims to explain the key differences between common servo / belt drive force feedback wheels, servo / gear drive force feedback wheels and newer direct drive force feedback wheels.
It's important to note that the term servo is widely misused in the racing simulation industry, causing the term to essentially mean nothing. It's unfortunate that these clever marketing gimmicks have won out in the minds of the consumer. Nonetheless, for the purpose of this article I will use the term as used in this market to prevent further confusion.
Servo & Belt Drive
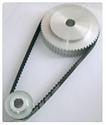
Servo and Belt drive systems utilize a belt and pulley system to help a smaller motor generate more torque. The steering wheel is NOT directly coupled to the motor shaft. Some Fanatec and Thrustmaster products fall into the category of Servo and Belt.
Servo & Belt Drive Advantages
Facilitates the use of low cost motors.
Belt dampens detail so smoothness is improved
Servo & Belt Drive Disadvantages
Belt absorbs force feedback detail resulting in less driving information being conveyed
Belt absorbs high frequency details
Belt wear and stretch result in increased maintenance and product failure
Low cost motor use dictates a pulley ratio that results in a loss of force feedback detail
Belt friction results in lost efficiency
Additional mass of pulleys must be overcome by the motor
Direct Drive
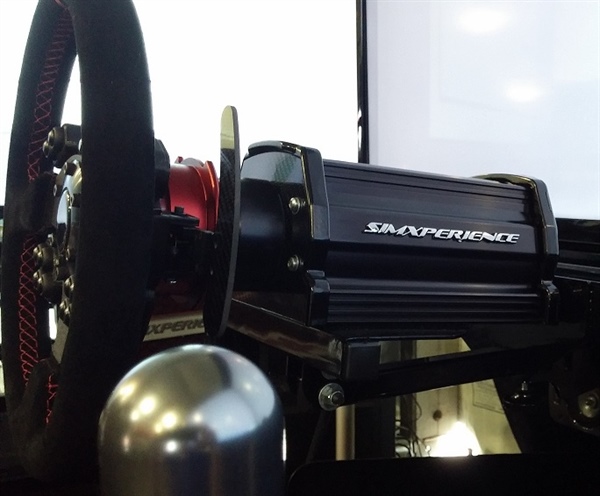
In a direct drive system, the steering wheel is directly coupled to the motor shaft. There are no gears or belts. Direct Drive wheels typically use larger motors to compensate for their lack of belts. The upcoming SimXperience AccuForce wheel is an example of a direct drive system.
Direct Drive Advantages
No loss of detail
No maintenance or belts to wear
True 1:1 performance
Ability to transmit high frequency detail
No additional drive train mass or inefficiency for motor to overcome
Direct Drive Disadvantages
Larger, more expensive motors are required
Servo & Gear Drive
To the best of my knowledge, there are currently no force feedback wheels on offer that purport to be a a servo and gear drive combination. That said, depending on your definition of "servo", the Logitech G25 may qualify. For the purpose of this article we'll be going by manufacturer claims so as to avoid confusion and Logitech does not claim the G25 as a servo system.
A deeper dive
It's no secret that SimXperience has chosen direct drive for the upcoming AccuForce product but the primary reason for our choice may surprise you and while stated above, may have escaped you!
'Low cost motor use dictates a pulley ratio that results in a loss of force feedback detail'
This is actually a quite troubling aspect of using a belt drive system. For the sake of argument, lets suppose a 20:1 pulley gear ratio for the belt drive system. While this ratio allows for the use of cheap motors, it's also the primary downfall. The belt drive motor would have to spin 20 times faster than the direct drive motor to match the direct drive systems ability to produce detail!
In a force feedback system, rapid motor direction changes are common. A direct drive system simply makes these changes and it's directly felt in the wheel.
The belt based system in our 20:1 example would need time to get up to the 20x faster speed it needs to match the direct drive system. However, in most cases, the motor will NOT get up to speed before the next force feedback instruction arrives. This means that it didn't accurately reproduce the data being provided to it by the vehicle simulation!
While many have commented on the smoothness of belt drive systems, I wonder how many realize that some portion of this smoothness is actually a loss of detail due to the belt and pulley gear ratio.
The Bottom Line
Belt drive is best suited to budget force feedback steering systems while Direct Drive is better suited to the high end wheel market where realism and accurate detail reproduction is required.
Check out our AccuForce Direct Drive Steering Wheel Ecosystem Here: Direct Drive Sim Steering Wheel Systems - AccuForce (simxperience.com)
Direct Drive vs Belt Drive vs Gear Drive